From the earliest ToF modules to lidar to the current DMS, they all use the near-infrared band:
TOF module (850nm/940nm)
LiDAR (905nm/1550nm)
DMS/OMS(940nm)
At the same time, the optical window is part of the optical path of the detector/receiver. Its main function is to protect the product while transmitting the laser of a specific wavelength emitted by the laser source, and collecting the corresponding reflected light waves through the window.
This window must have the following basic functions:
1. Visually appears black to cover the optoelectronic devices behind the window;
2. The overall surface reflectivity of the optical window is low and will not cause obvious reflection;
3. It has good transmittance for the laser band. For example, for the most common 905nm laser detector, the transmittance of the window in the 905nm band can reach more than 95%.
4. Filter harmful light, improve the signal-to-noise ratio of the system, and enhance the detection capability of lidar.
However, LiDAR and DMS are both automotive products, so how the window products can meet the requirements of good reliability, high transmittance of the light source band, and black appearance has become a problem.
01. Summary of window solutions currently on the market
There are mainly three types:
Type 1: The substrate is made of infrared penetrating material
This type of material is black because it can absorb visible light and transmit near-infrared bands, with a transmittance of about 90% (such as 905nm in the near-infrared band) and an overall reflectivity of about 10%.
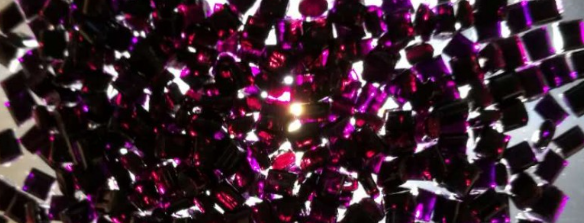
This type of material can use infrared highly transparent resin substrates, such as Bayer Makrolon PC 2405, but the resin substrate has poor bonding strength with the optical film, cannot withstand harsh environmental testing experiments, and cannot be plated with highly reliable ITO transparent Conductive film (used for electrification and defogging), so this type of substrate is usually uncoated and used in non-vehicle radar product windows that do not require heating.
You can also choose SCHOTT RG850 or Chinese HWB850 black glass, but the cost of this type of black glass is high. Taking the HWB850 glass as an example, its cost is more than 8 times that of ordinary optical glass of the same size, and most of this type of product cannot pass the ROHS standard and therefore cannot be applied to mass-produced lidar windows.
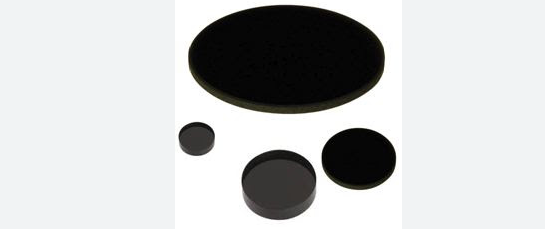
Type 2: using infrared transmissive ink
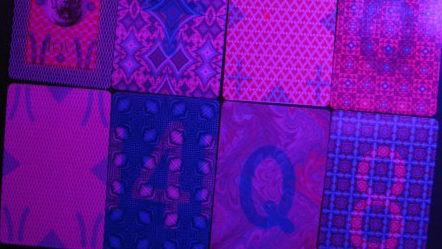
This type of infrared penetrating ink absorbs visible light and can transmit near-infrared bands, with a transmittance of about 80% to 90%, and the overall transmittance level is low. Moreover, after the ink is combined with the optical substrate, the weather resistance cannot pass the strict automotive weather resistance requirements (such as high temperature tests), so infrared penetrating inks are mostly used in other products with low weather resistance requirements such as smart phones and infrared cameras.
Type 3: using black coated optical filter
The black coated filter is a filter that can block visible light and has high transmittance at the NIR band (such as 905nm).
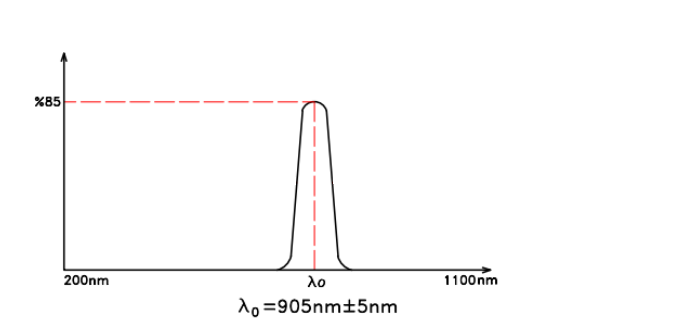
The black coated filter is designed with silicon hydride, silicon oxide and other thin film materials, and is prepared using magnetron sputtering technology. It is characterized by stable and reliable performance and can be mass-produced. At present, conventional black optical filter films generally adopt a structure similar to a light-cutoff film. Under the conventional silicon hydride magnetron sputtering film forming process, the usual consideration is to reduce the absorption of silicon hydride, especially the absorption of the near-infrared band, to ensure a relatively high transmittance in the 905nm band or other lidar bands such as 1550nm.
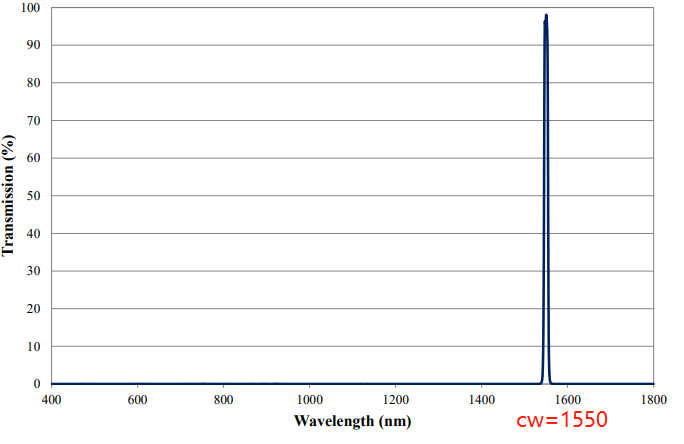
Post time: Nov-22-2024